As the electric vehicle (EV) revolution accelerates, the build-out of robust charging infrastructure has become a critical focus for businesses and municipalities. While initial deployment costs are significant, the long-term profitability and sustainability of an EV charging station network heavily depend on managing ongoing operational expenditures, chief among them being maintenance costs. These expenses can silently erode margins if not proactively addressed.
Optimizing charging infrastructure O&M (Operations and Maintenance) isn't just about fixing broken chargers; it's about maximizing uptime, enhancing user experience, extending asset life, and ultimately, boosting the bottom line. Simply reacting to failures is a costly approach. We will delves into effective strategies to significantly reduce maintenance costs, ensuring your charging station assets deliver maximum value.
Understanding Your Maintenance Cost Landscape
To effectively reduce maintenance costs, you must first understand where they originate. These costs are typically a mix of planned and unplanned expenditures.
Common contributors to EV charging station maintenance costs include:
1.Hardware Failures: Malfunctions of core components like power modules, connectors, displays, internal wiring, or cooling systems. These require skilled technicians and parts replacement.
2.Software and Connectivity Issues: Bugs, outdated firmware, network communication loss, or platform integration problems that prevent chargers from operating or being managed remotely.
3.Physical Damage: Accidents (vehicle collisions), vandalism, or environmental damage (extreme weather, corrosion). Repairing or replacing physically damaged units is expensive.
4.Preventive Maintenance Activities: Scheduled inspections, cleaning, testing, and calibration. While an expenditure, this is an investment to avoid higher costs later.
5.Labor Costs: Technicians' time for travel, diagnosis, repair, and routine checks.
6.Spare Parts & Logistics: Cost of replacement parts and the logistics involved in getting them to the site quickly.
According to various industry reports (like those from consulting firms analyzing EV charging markets), O&M can account for a significant portion of the Total Cost of Ownership (TCO) over a charger's lifespan, potentially ranging from 10% to 20% or even higher depending on location, equipment quality, and management practices.
Core Strategies to Drive Down Maintenance Costs
Proactive and intelligent management is key to transforming EV charging station maintenance from a major expense into a manageable operational cost. Here are proven strategies:
1. Strategic Equipment Selection: Buy Quality, Reduce Future Headaches
The cheapest charger upfront is rarely the most cost-effective in the long run when considering operational costs.
• Prioritize Reliability: Invest in chargers with a proven track record of reliability and low failure rates. Look for certifications (e.g., UL in the US, CE in Europe) and adherence to relevant standards, which indicate quality and safety testing.Elinkpower's authoritative certificates include ETL, FCC, Energy Star, CSA, CE, UKCA, TR25 and so on, and we are your trustworthy partner.
• Assess Environmental Resilience: Choose equipment designed to withstand local climate conditions – extreme temperatures, humidity, salt spray (coastal areas), etc. Look at the equipment's IP (Ingress Protection) rating. Elinkpower's charging post protection level ik10, ip65, greatly protects the safety of the post, prolongs the service life and reduces costs
• Standardization: Where possible, standardize on a few reliable charger models and suppliers across your network. This simplifies spare parts inventory, technician training, and troubleshooting.
• Evaluate Warranty and Support: A comprehensive warranty and responsive technical support from the manufacturer can significantly reduce your direct repair costs and minimize downtime.Elinkpower offers a 3-year warranty, as well as remote upgrade services.
2. Embrace Preventive Maintenance: A Little Effort Saves a Lot
Shifting from a reactive "fix-it-when-it-breaks" approach to proactive preventive maintenance is perhaps the single most impactful strategy for reducing maintenance costs and improving charger reliability.
Studies and industry best practices from organizations like NREL (National Renewable Energy Laboratory) in the US and various European initiatives emphasize that regular checks can catch issues before they cause failure, preventing more extensive and expensive repairs, and significantly reducing unplanned downtime.
Key preventive maintenance activities include:
• Routine Visual Inspections: Checking for physical damage, wear and tear on cables and connectors, clear ventilation ports, and legible displays.
• Cleaning: Removing dirt, dust, debris, or insect nests from external surfaces, vents, and connector holsters.
• Electrical Checks: Verifying proper voltage and current output, checking terminal connections for tightness and corrosion (should be done by qualified personnel).
• Software/Firmware Updates: Ensuring the charger and network software are running the latest stable versions for optimal performance and security.
3. Leverage Remote Monitoring & Diagnostics: Get Smart About Issues
Modern networked chargers offer powerful capabilities for remote management. Maximizing the use of your charging management software platform is crucial for efficient O&M.
• Real-time Status Monitoring: Gain instant visibility into the operational status of every charger in your network. Know which chargers are active, idle, or offline.
• Automated Alerts and Notifications: Configure the system to send immediate alerts for errors, faults, or performance deviations. This allows for rapid response, often before users even report an issue.
• Remote Troubleshooting and Diagnostics: Many software issues or minor glitches can be resolved remotely through reboots, configuration changes, or firmware pushes, avoiding the need for a costly site visit.
• Data-Driven Predictive Maintenance: Analyze data patterns (charging sessions, error logs, voltage fluctuations, temperature trends) to predict potential component failures before they occur. This allows for scheduled maintenance during low-usage periods, minimizing downtime and operational costs.
Reactive vs. Proactive (Smart) Maintenance
Feature | Reactive Maintenance | Proactive (Smart) Maintenance |
---|---|---|
Trigger | User report, complete failure | Automated alert, data anomaly, schedule |
Response | Emergency, often requires site visit | Planned or rapid remote action |
Diagnosis | Primarily on-site troubleshooting | Remote diagnostics first, then targeted on-site |
Downtime | Longer, unplanned, revenue loss | Shorter, planned, minimal revenue loss |
Cost | Higher per incident | Lower per incident, reduced overall |
Asset Lifespan | Potentially shortened due to stress | Extended due to better care |
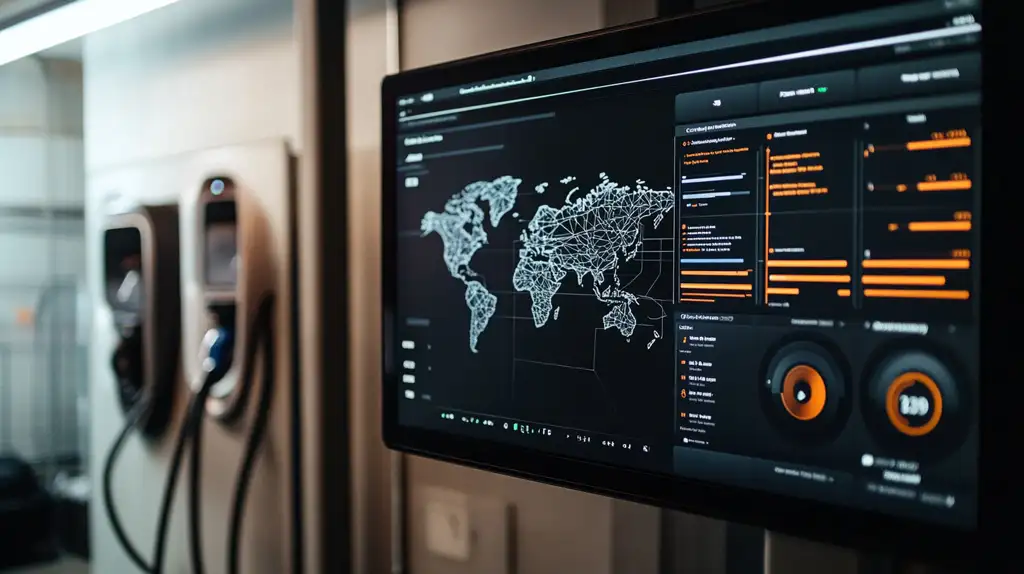
4. Optimize Operations & Supply Chain Management
Efficient internal processes and strong vendor relationships contribute significantly to lowering maintenance costs.
• Streamlined Workflow: Implement a clear, efficient workflow for identifying, reporting, dispatching, and resolving maintenance issues. Use a Computerized Maintenance Management System (CMMS) or the management platform's ticketing system.
• Spare Parts Inventory: Maintain an optimized inventory of critical spare parts based on historical failure data and supplier lead times. Avoid stockouts that cause downtime, but also avoid excessive inventory that ties up capital.
• Vendor Relationships: Build strong partnerships with your equipment suppliers and potentially third-party maintenance providers. Negotiate favorable service level agreements (SLAs), response times, and parts pricing.
5. Invest in Skilled Technicians & Training
Your maintenance team is on the front lines. Their expertise directly impacts the speed and quality of repairs, affecting maintenance costs.
• Comprehensive Training: Provide thorough training on the specific charger models you operate, covering diagnostics, repair procedures, software interfaces, and safety protocols (working with high-voltage equipment requires strict safety measures).
• Focus on First-Time Fix Rate: Higher skilled technicians are more likely to diagnose and fix the issue correctly on the first visit, reducing the need for costly follow-up visits.
• Cross-Training: Train technicians on multiple aspects (hardware, software, networking) if possible, to increase their versatility.
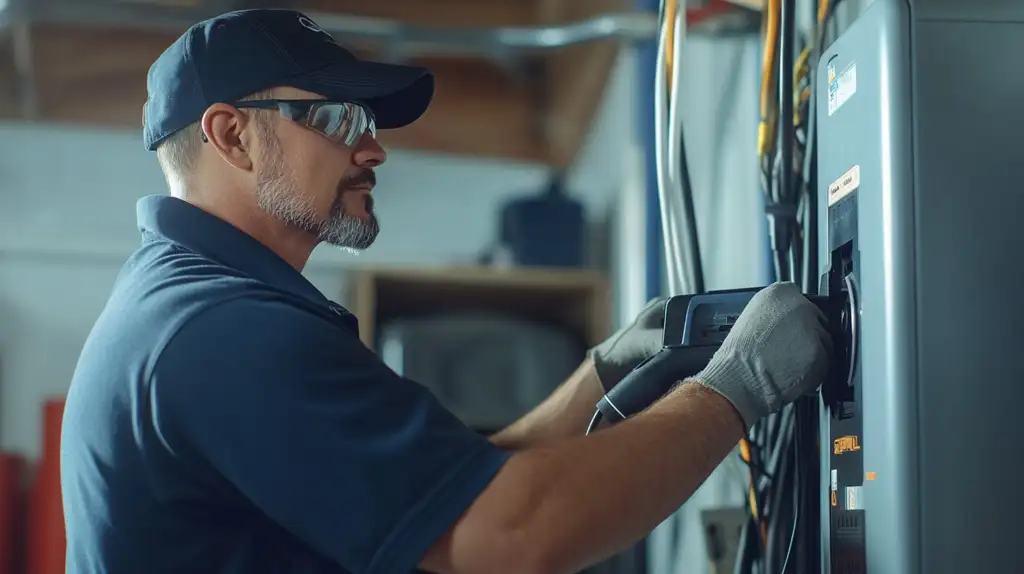
6. Proactive Site Management & Physical Protection
The physical environment of the charging station plays a significant role in its longevity and susceptibility to damage.
• Strategic Placement: During planning, choose locations that minimize the risk of accidental impact from vehicles while ensuring accessibility.
• Install Protective Barriers: Use bollards or wheel stops to physically protect chargers from low-speed vehicle impacts in parking spaces.
• Implement Surveillance: Video surveillance can deter vandalism and provide evidence if damage occurs, potentially aiding in cost recovery.
• Keep Sites Clean and Accessible: Regular site visits to clean up trash, clear snow/ice, and ensure clear access paths help maintain equipment and improve user experience.
The Compelling Benefits: Beyond Just Savings
Successfully implementing these strategies to lower maintenance costs yields significant benefits beyond the immediate savings:
• Increased Uptime & Revenue: Reliable chargers mean more charging sessions and higher revenue generation. Reduced unplanned downtime directly translates to increased profitability.
• Enhanced Customer Satisfaction: Users rely on chargers being available and functional. High reliability leads to positive user experiences and builds customer loyalty.
• Extended Asset Lifespan: Proper maintenance and timely repairs prolong the operational life of your expensive charging infrastructure assets, maximizing your initial investment.
• Improved Operational Efficiency: Streamlined processes, remote capabilities, and skilled staff make your O&M team more productive.
Electric vehicle charging station maintenance costs are a critical factor in the long-term success and profitability of charging networks in the US, Europe, and globally. Simply reacting to failures is a costly and unsustainable model.
By strategically investing in quality equipment upfront, prioritizing preventive maintenance, leveraging the power of remote monitoring and data analytics for predictive insights, optimizing operational workflows, fostering a skilled maintenance team, and proactively managing site environments, operators can take control of their O&M expenditures.
Implementing these proven strategies will not only significantly reduce maintenance costs but also lead to increased charger reliability, higher uptime, greater customer satisfaction, and ultimately, a more profitable and sustainable EV charging station business. It's time to move from reactive spending to proactive investment in operational excellence.
As an enterprise deeply rooted in the field of electric vehicle charging equipment manufacturing for many years, Elinkpower possesses not only extensive production experience but also profound insights and practical experience regarding the real-world O&M challenges faced by charging stations, especially in maintenance cost control. We channel this valuable O&M experience back into our product design and manufacturing, committing to creating highly reliable, easy-to-maintain EV chargers that help you reduce maintenance costs right from the start. Choosing Elinkpower means partnering with a company that integrates quality with future operational efficiency.
Want to discover how Elinkpower, through our expertise and innovative solutions, can help you effectively reduce EV charging station maintenance costs and significantly improve your operational costs efficiency? Contact our team of experts today to plan your smarter, more cost-effective charging infrastructure future!
Frequently Asked Questions
• Q: What is the biggest factor contributing to high EV charging station maintenance costs?
A: Often, the biggest contributor is unplanned, reactive repairs resulting from hardware failures that could have been prevented with proactive preventive maintenance and better initial equipment selection.
• Q: How can remote monitoring help me save money on maintenance?
A: Remote monitoring enables early fault detection, remote diagnostics, and sometimes even remote fixes, reducing the need for costly site visits and enabling more efficient scheduling of necessary on-site work.
• Q: Is investing in expensive chargers upfront worth it for lower maintenance costs? A: Yes, generally. While upfront cost is higher, reliable, quality equipment typically has lower failure rates and lasts longer, leading to significantly lower operational costs and higher uptime over its lifespan compared to cheaper, less reliable options.
• Q: How often should preventive maintenance be performed on EV chargers?
A: The frequency depends on the equipment type, usage volume, and environmental conditions. Following the manufacturer's recommended maintenance schedule is a good starting point, often involving quarterly or annual inspections and cleaning.
• Q: Beyond technical skills, what's important for a maintenance technician working on EV chargers?
A: Strong diagnostic skills, adherence to strict safety protocols (especially when working with high voltage), good record-keeping, and the ability to utilize remote monitoring tools are crucial for efficient and safe O&M.
Authoritative Source Links:
1.National Renewable Energy Laboratory (NREL) - Reliability of Public EV Charging Infrastructure: https://www.nrel.gov/docs/fy23osti0.pdf
2.ChargeUp Europe - Position Paper: Policy Recommendations for a Smoother Roll-out of Charging Infrastructure: https://www.chargeupeurope.eu/publications/position-paper-policy-recommendations-for-a-smoother-roll-out-of-charging-infrastructure
3.European Environment Agency (EEA) - Reports related to transport and environment: https://www.eea.europa.eu/publications/transport-and-environment-report-2021
4.SAE International or CharIN Standards (related to charging interfaces/reliability): https://www.sae.org/standards/selectors/ground-vehicle/j1772 (SAE J1772 is a US standard for connectors, relevant to hardware reliability and interoperability). https://www.charin.global/ (CharIN promotes the CCS standard used in US/Europe, also relevant to ensuring reliable connections). Referencing the importance of adhering to such standards implicitly supports the 'quality equipment' strategy.
Post time: May-13-2025